The ability to move fluids efficiently, safely, and reliably is critical in industries ranging from chemical processing to wastewater management. Enter the double diaphragm pump, a workhorse of fluid transfer technology.
Also known as an Air-Operated Double Diaphragm (AODD) pump, this device has earned its reputation as a versatile, durable, and user-friendly solution for handling everything from viscous slurries to corrosive chemicals.
But what exactly is a double diaphragm pump, and how does it operate? This article breaks down its design, working principles, and advantages to explain why it’s a go-to choice across countless applications.
Key Components of a Double Diaphragm Pump
A double diaphragm pump consists of several essential parts that work in harmony to move fluids:
- Diaphragms: Two flexible diaphragms, typically made of elastomers (e.g., rubber, Santoprene) or thermoplastics, act as barriers between the pumped fluid and the compressed air driving the system. Learn more about diaphragm pumps at KNF.
- Air Valve: This central component directs compressed air alternately to the backside of each diaphragm, creating the pump’s reciprocating motion.
- Chambers: Each diaphragm is housed in a liquid chamber that draws in and expel fluid.
- Check Valves: Ball or flap valves at the inlet and outlet of each chamber ensure one-way flow, preventing backflow during operation.
- Manifold: Connects the pump to the fluid intake and discharge lines.
The pump’s construction materials are chosen based on the fluid’s properties—corrosion-resistant metals or plastics for harsh chemicals, and food-grade materials for sanitary applications.
How It Works
The AODD pump operates through a simple yet ingenious reciprocating cycle powered by compressed air. Here’s a step-by-step breakdown:
1. Air Distribution Phase
Compressed air enters the air valve and is directed to the backside of Diaphragm A, forcing it inward. This pressurizes Chamber A, pushing the fluid out through the discharge check valve.
Simultaneously, the movement of Diaphragm A pulls Diaphragm B outward via a connected shaft, creating a vacuum in Chamber B. This vacuum opens the inlet check valve, drawing fluid into Chamber B.
2. Stroke Reversal
Once Diaphragm A completes its stroke, the air valve shifts the airflow to the backside of Diaphragm B. Now, Chamber B pressurizes, expelling its fluid, while Diaphragm A retracts to fill Chamber A with new fluid.
3. Continuous Cycling
This alternating action repeats, creating a pulsating flow that moves fluid consistently. The cycle speed can be adjusted by regulating the air supply pressure, allowing operators to control the flow rate.
The pump is self-priming, meaning it can evacuate air from the intake line and start moving fluid without manual intervention, even if the source is below the pump.
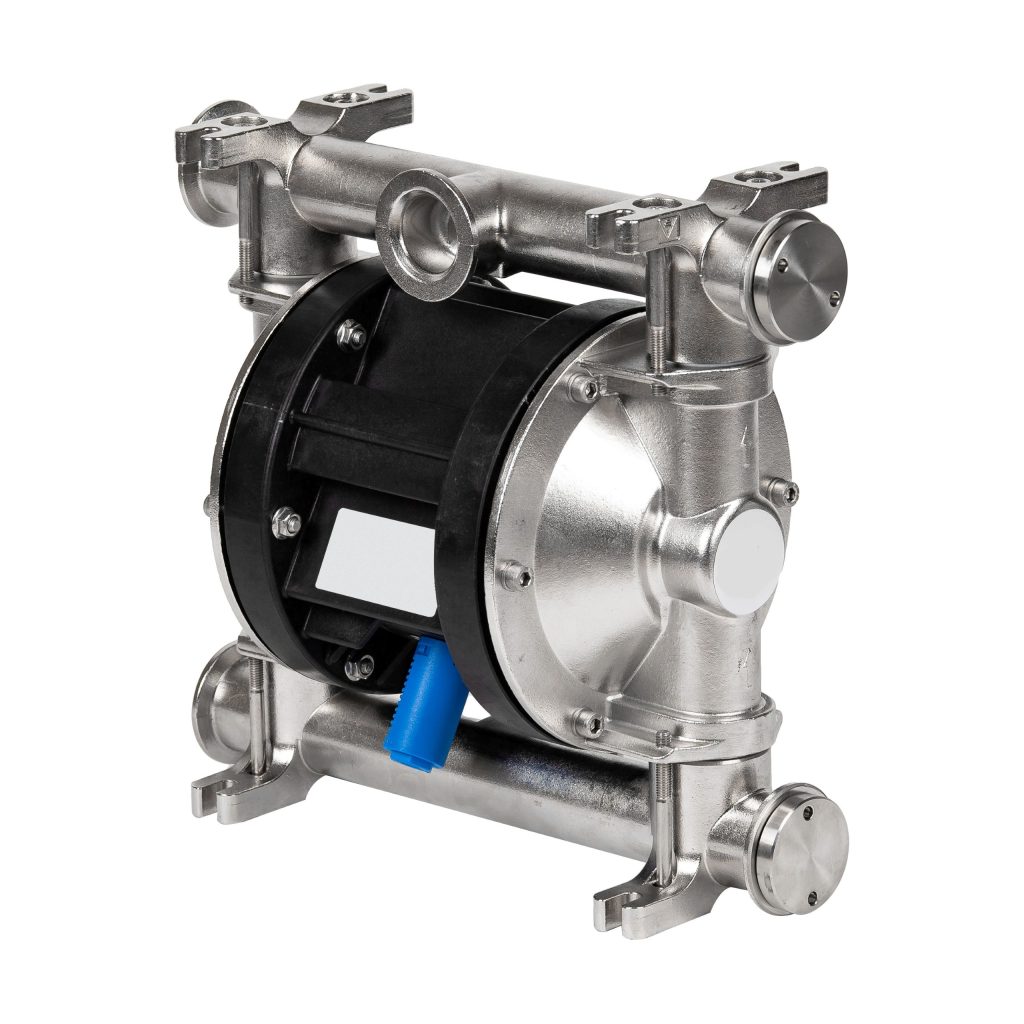
Applications Across Industries
Below, we explore how its features address specific challenges in each sector, driving efficiency and reliability through tailored applications.
Chemical Processing
Double diaphragm pumps are indispensable for transferring aggressive substances like acids, solvents, and caustic solutions. Its air-operated design eliminates sparks, making them inherently safe for volatile environments where flammable or explosive materials are present.
These pumps also excel in metering exact volumes of additives or catalysts during batch processes. For example, they are widely used to transfer chlorine dioxide in water treatment systems without corroding metal components, ensuring both safety and efficiency.
Wastewater Treatment
Wastewater treatment facilities rely on double diaphragm pumps to handle thick sludge, grit-laden liquids, and abrasive mixtures that would damage conventional pumps. Its ability to pass solids up to 3/8 inches in diameter reduces clogging during critical processes like grit removal or sludge transfer.
Durability is further enhanced by abrasion-resistant materials like natural rubber diaphragms, which withstand prolonged exposure to sand, rocks, and debris. A common application includes pumping lime slurry to neutralize acidic wastewater, where traditional pumps might fail due to valve clogging or wear.
Food and Beverage
Constructed with stainless steel and FDA-approved elastomers, these pumps meet stringent sanitary standards of food and beverage. Its gentle pumping action preserves the texture and structure of shear-sensitive products such as yogurt, custards, and fruit purees, avoiding the breakdown of delicate solids.
Easy disassembly supports Clean-in-Place (CIP) protocols, enabling thorough sanitation between batches to prevent cross-contamination. For instance, these pumps are often used to transfer high-viscosity chocolate in confectionery production lines, maintaining its smooth consistency without altering quality.
Mining and Construction
Mining and construction sectors demand equipment capable of enduring extreme conditions, and double diaphragm pumps rise to the challenge. Its ability to handle thick, abrasive mixtures like cement grout makes them indispensable for vertical or long-distance pumping in construction projects.
Portability is another key advantage—lightweight and compact designs allow easy transport between remote job sites, often without requiring external power sources. A notable example includes injecting grout into unstable soil during tunneling projects to reinforce structures and prevent collapses.
Pharmaceuticals
Pharmaceutical manufacturing requires contamination-free fluid handling, and double diaphragm pumps deliver precision and sterility for critical processes. Sealed, crevice-free designs prevent microbial growth, while materials like EPDM or PTFE meet USP Class VI standards for biocompatibility, ensuring safe transfer of active pharmaceutical ingredients (APIs) and sterile solutions.
Adjustable air pressure enables precise dosing for tasks like filling vials or blending sensitive formulations. Additionally, autoclavable components withstand high-temperature sterilization processes, which are essential for producing injectables or vaccines. An example includes metering ethanol-based sanitizers into sterile packaging without generating particles that could compromise product quality.
Compared to peristaltic pumps, double diaphragm pumps require less maintenance—eliminating the need for frequent tubing replacements—and provide greater durability in abrasive environments. They also outperform gear pumps in safety and versatility, as they can run dry without seizing and are gentler on shear-sensitive fluids.
Bottom Line
The double diaphragm pump stands out as a remarkably flexible and robust solution for fluid transfer challenges. As innovations like energy-efficient smart air valves and hybrid diaphragms emerge, these pumps will continue to evolve, reinforcing their role as an industrial mainstay.