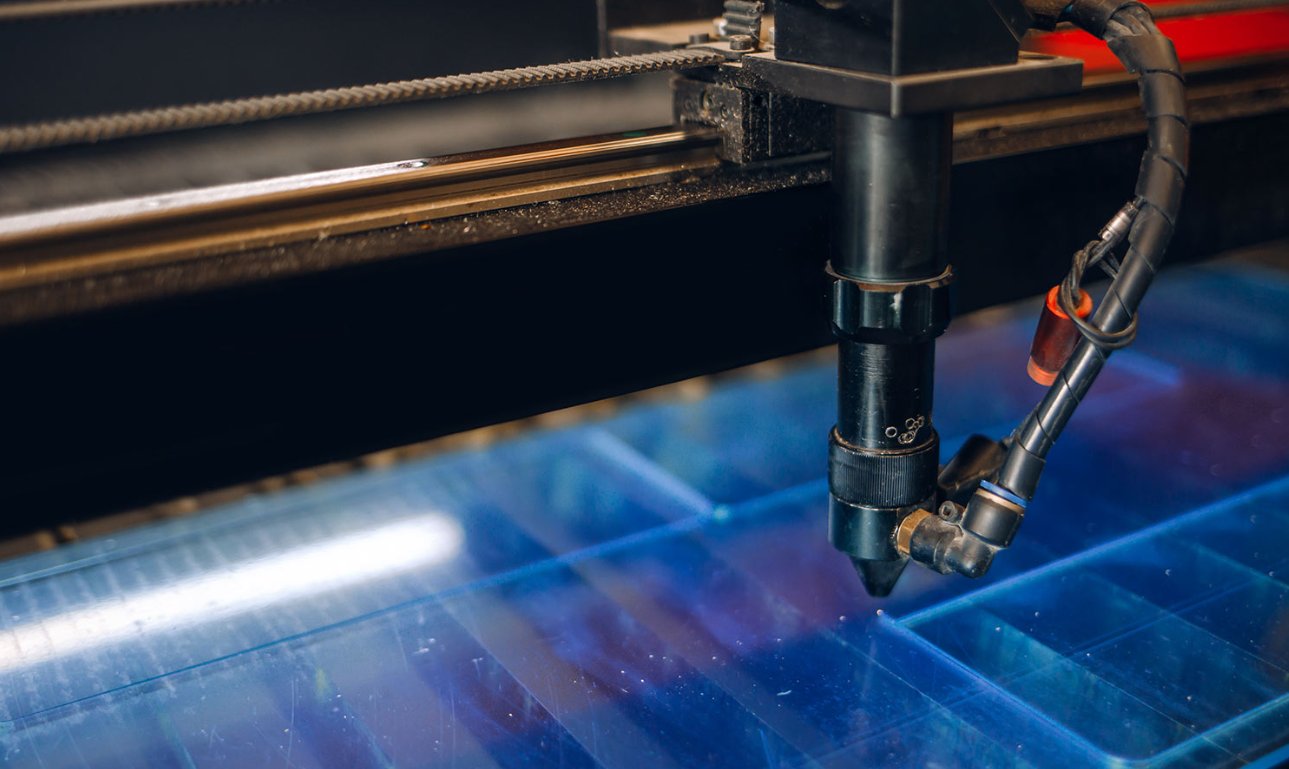
People have used plastics and plastic composites to manufacture various items, including industrial and personal protective equipment, technological devices, workplace accessories and other everyday items.
Despite their core material being the same, production and manufacturing procedures may vary across industries and purposes. Plastic is a cost-effective and easily malleable material, which allows businesses to quickly and efficiently mass-produce various products with varying specifications.
What Plastic Fabrication Processes Are There?
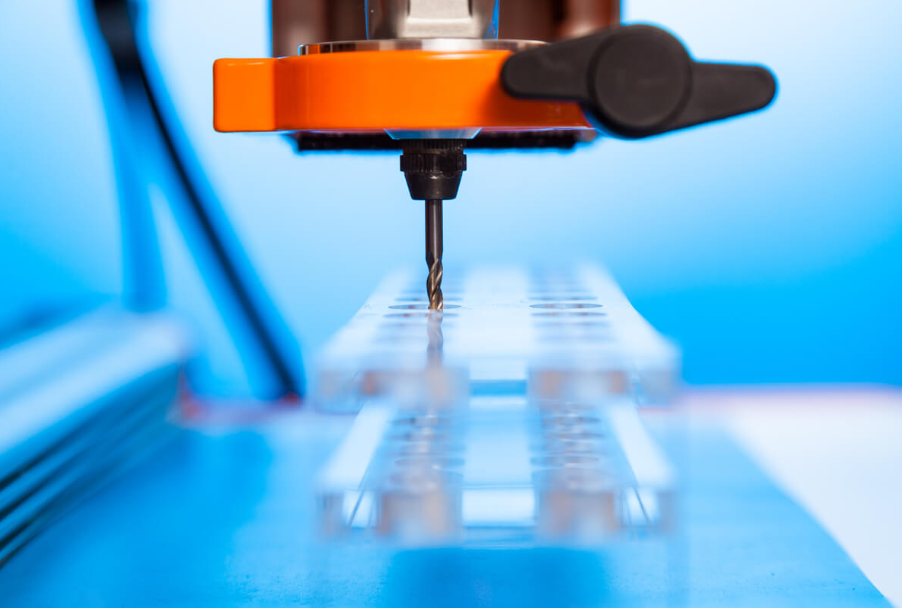
The manufacturing industry is rapidly evolving and businesses expect quick and reliable lead times to promptly address market demands. Nowadays, there are several efficient and industry-leading plastics fabrication processes for streamlined production and higher customer satisfaction.
Plastic Bending
The first process relies on ABS’ strength and flexibility – manufacturers shape and bend thermoplastics along a defined line until they reach their intended shape. Once the material cools down, it retains its newfound form without any adhesives or additional fasteners.
Temperature control is one of the key things at play during this plastics fabrication process. Overheating ABS can lead to warping or discolouration, while underheating could result in poor beds or damage to the plastic itself.
Other key elements include material thickness which determines the time and energy required to heat up evenly and angle precision, which includes jigs or clamps to maintain consistent angles throughout the bend.
Some of the key advantages of this process are its high precision and tolerance, minimal damage to the material’s core structure and smooth bending transitions for more polished surfaces.
CNC Machining
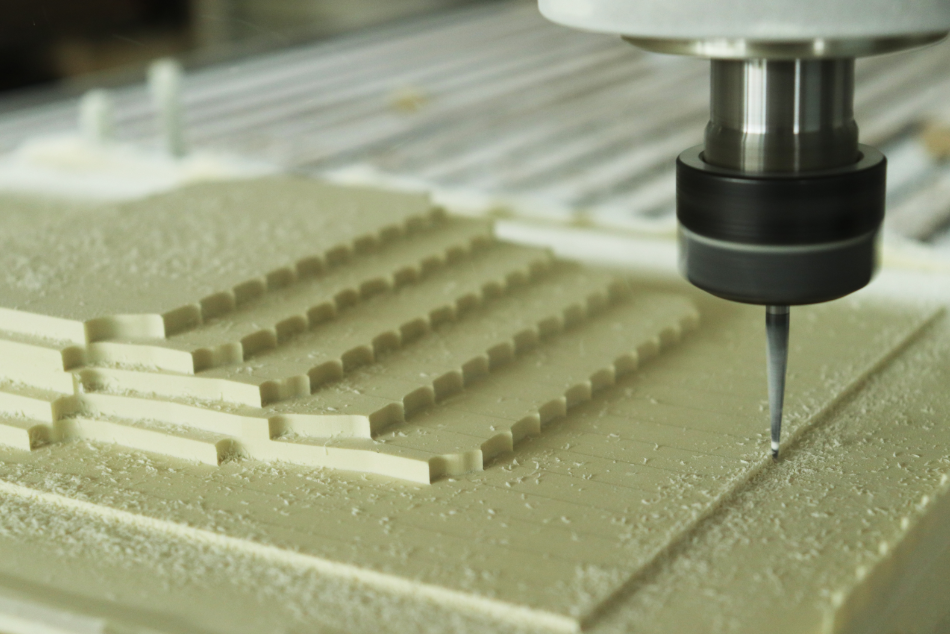
Computer Numerical Control (CNC) machining is an advanced plastic fabrication method that relies on computer commands to control cutting tools and machinery. Businesses can easily automate these processes for precise, repeatable and efficient manufacturing processes.
The entire technique starts with Computer-Aided Design (CAD) and Computer-Aided Manufacturing (CAM) models that guide the machine’s movements. You can select the required plastic and let the cutting, milling or grinding tools shape it into the necessary designs.
Of course, this is a rough production method and you may need additional deburring, polishing or coating to achieve optimal results.
But even so, this method supports various shapes, undercuts and 3D contours which are crucial for complex designs and functional components. It’s compatible with various plastics and can automate repetitive processes, which in turn, saves you time and boosts productivity.
However, some businesses may see the initial higher costs as a drawback and may not have adequate resources to train skilled operators to use the machines.
Moreover, subtractive processes may produce more waste than additive manufacturing methods, which can be a concern for more eco-conscious brands.
Laser Cutting
Continuing the list of plastic fabrications is a high-powered laser beam that slices, engraves and etches plastic materials with exceptional accuracy. Since it’s a non-contact process and the laser never actually touches the material, it reduces wear and tear on tools and minimizes damage to end products.
Laser cutting is quite similar to CNC machining in the sense that it all starts with a digital file that’s loaded onto the system, often containing a vector-based CAD design. Manufacturers position plastic sheets or pieces on the machine’s cutting bed and secure them with clamps or vacuum systems to prevent movement.
Once everything’s in place, the laser uses intense lights to vaporize the plastic along the programmed path while ensuring a minimal heat-affected zone. This way, the machine prevents warping or deformation and helps ABS retain its intended shape.
When the cutting stage is finished, you won’t need to smooth out the edges or take additional finishing steps. If you’re engraving, the laser itself results in clean, sharp designs on the plastic’s surface.
Given the precise and non-contact nature of this procedure, laser cutting is quite useful for manufacturing acrylic signage and custom display stands with polished edges. You can also use them to engrave logos or intricate designs onto plastic packaging or create detailed prototypes for engineering or architecture purposes.
Flame Polishing
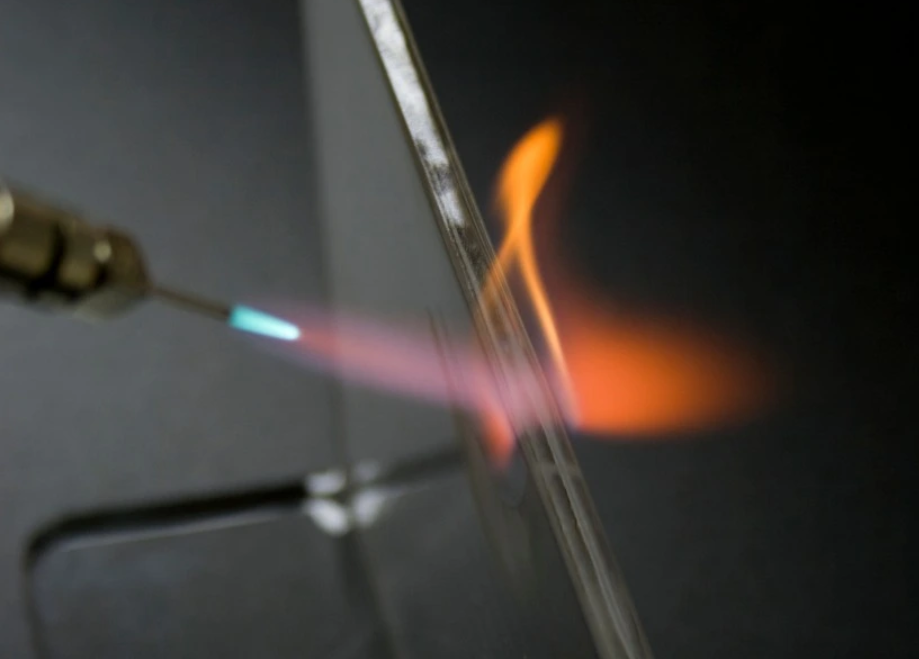
The next technique is a finishing process that results in smooth and polished thermoplastic surfaces. Manufacturers can apply a controlled flame to the material’s surface to remove imperfections like rough edges, accidental scratches and tool marks. The heat melts away all the blemishes to relevel a glossy, transparent finish.
To start the process, you’d need to cut, shape or machine the plastic material into the desired form. Make sure to clean and deburr the edges to remove larger imperfections and prepare the surface.
Next, you can use a high-temperature flame, usually from a hydrogen-oxygen torch, to carefully pass over the plastic’s edges and soften the surface. Once the material cools down naturally, it reveals a clear, glossy finish which you can further inspect for consistency and avoid distortions.
This method’s smooth and glossy results with optical clarity are perhaps its strongest selling points because businesses can then use the same plastics for retail displays, museum showcases and trophy collections. Brands can also use it for lenses, light guides, jewellery or other acrylic creations.
Moreover, it’s a much more efficient process than manual polishing and requires minimal labour for admirable results. Not to mention the minimal abrasive wear and tear it causes thanks to the lack of physical contact between the tools and plastics.
Vacuum Forming
Finally, vacuum forming shapes thermoplastic sheets into three-dimensional forms by applying controlled heat and vacuum pressure. This results in lightweight, durable and scalable plastic components, which businesses can use for prototyping or mass production across various industries.
Getting started with the procedure involves clamping a thermoplastic sheet securely onto the vacuum-forming machine and then heating it up until it reaches its softening point. At this time, it becomes pliable enough for shaping and moulding into the desired end product.
You can place the heated plastic over a mould, and apply vacuum pressure to pull the material tightly around its surface. When the plastic cools down and solidifies, it maintains its newfound shape and you can trim excess material to get the final product.
One of the biggest advantages of this process is its budget-friendly implications and quick turnaround times. Businesses can manufacture various plastic items in fast production cycles and reduced lead times.
Not to mention the eco-friendly implications this has, since most thermoplastics used in vacuum forming are fully recyclable. This minimizes waste and contributes to more efficient trimming. Plus, this method is quite scalable, so it supports both small batches and large-scale production runs.